Spiral bevel gears and hypoid gears are two specialized types of gears widely used in power transmission systems, especially in automotive, industrial, and aerospace applications. Both types allow for the transfer of power between non-parallel shafts, typically at a 90-degree angle. However, they differ in design, performance, and applications.
Spiral Bevel Gears feature a cone-shaped structure with spiral-shaped teeth, allowing for a smoother and quieter engagement compared to traditional straight bevel gears. The spiral design enables gradual tooth engagement, reducing shock and vibration, which is advantageous for applications requiring stability and reduced noise. Spiral bevel gears are capable of handling relatively high speeds and torques and are often used in applications like automotive differentials, where smooth and precise power transfer is essential. Due to their high load-carrying capacity and efficiency, they are also found in industrial machinery, robotics, and other equipment that require a 90-degree transmission of power with high accuracy.
Related Products
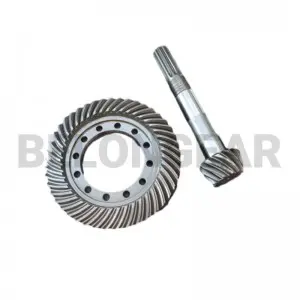
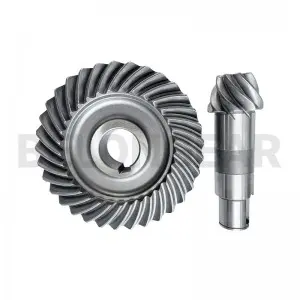
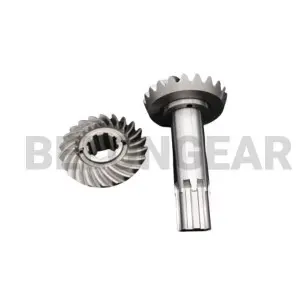
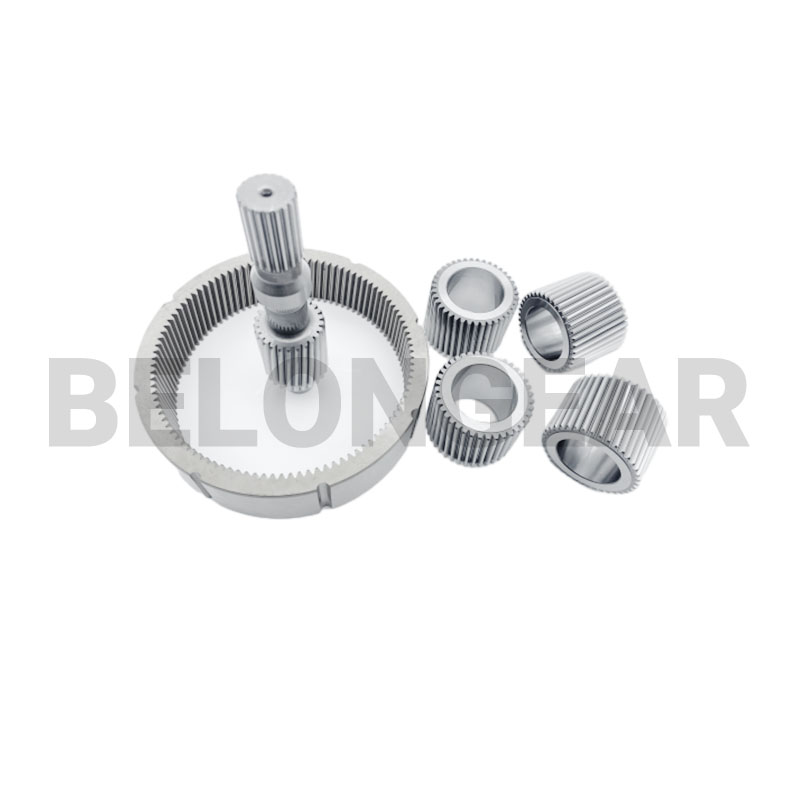

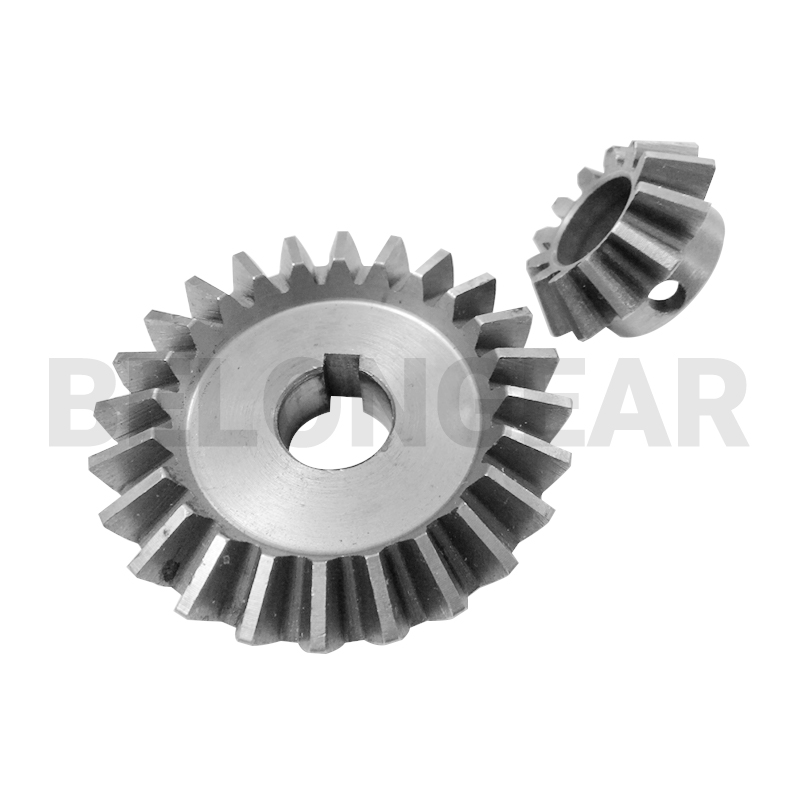
Hypoid Gears, on the other hand, share a similar spiral tooth design but differ in that the gear shafts do not intersect. The hypoid gear’s pinion is offset relative to the gear centerline, creating a hyperboloid shape. This offset allows hypoid gears to support greater torque than spiral bevel gears and provides additional advantages in automotive applications. For example, in rear-wheel-drive vehicles, hypoid gears enable the drive shaft to sit lower, reducing the vehicle’s center of gravity and allowing more interior space. The offset design also allows for smoother and quieter operation, making hypoid gears particularly desirable in high-load applications such as trucks and heavy machinery.
Manufacturing hypoid gears is complex and requires precise machining and surface treatments to ensure durability and performance under heavy loads. The choice between spiral bevel and hypoid gears depends on the specific requirements of the application, including load, speed, and design constraints. Both gear types are integral to modern machinery and continue to evolve with advances in manufacturing technology.