Wide Range of cylindrical gears from Module 0.5-30 for spur gears ,helical gears ,ring gears ,worm gears
HELICAL GEARS MANUFACTURING PROCESS
Helical Gear Manufacturing: Unlocking Efficiency in Mechanical Transmission
In the realm of modern mechanical design, helical gears stand out as a critical component in achieving smooth and efficient power transmission. At Shanghai Belon Machinery Co., Ltd, we specialize in the manufacturing of high-precision helical gears, offering solutions that enhance the performance and reliability of mechanical systems. In this article, we’ll delve into the fundamentals of helical gears, our manufacturing process, and their diverse applications across various industries
What Are Helical Gears?
Helical gears are a type of gear with teeth that are cut at an angle to the axis of rotation, creating a helix shape. This design contrasts with the straight teeth found in spur gears and provides several advantages, including improved contact strength and smoother operation. The helical gear’s unique tooth engagement ensures quieter operation and greater efficiency, making it ideal for high-speed and high-load applications.
Benefits of Helical Gears
- Smooth Operation: The angled teeth of helical gears engage gradually, resulting in a smoother transfer of power. This reduces noise and vibration, contributing to a quieter and more comfortable operation.
- Increased Efficiency: Helical gears have a larger contact area compared to spur gears, which reduces friction and improves power transmission efficiency. This helps in conserving energy and enhances overall system performance.
- Higher Load Capacity: The helical design distributes the load more evenly across the teeth, allowing these gears to handle higher loads and stresses. This increases the gear’s lifespan and reduces maintenance requirements.
Certainly! Here's a sample article about Helical Gear Manufacturing for a company website:
Helical Gear Manufacturing: Unlocking Efficiency in Mechanical Transmission
In the realm of modern mechanical design, helical gears stand out as a critical component in achieving smooth and efficient power transmission. At [Your Company Name], we specialize in the manufacturing of high-precision helical gears, offering solutions that enhance the performance and reliability of mechanical systems. In this article, we’ll delve into the fundamentals of helical gears, our manufacturing process, and their diverse applications across various industries.
What Are Helical Gears?
Helical gears are a type of gear with teeth that are cut at an angle to the axis of rotation, creating a helix shape. This design contrasts with the straight teeth found in spur gears and provides several advantages, including improved contact strength and smoother operation. The helical gear’s unique tooth engagement ensures quieter operation and greater efficiency, making it ideal for high-speed and high-load applications.
Benefits of Helical Gears
- Smooth Operation: The angled teeth of helical gears engage gradually, resulting in a smoother transfer of power. This reduces noise and vibration, contributing to a quieter and more comfortable operation.
- Increased Efficiency: Helical gears have a larger contact area compared to spur gears, which reduces friction and improves power transmission efficiency. This helps in conserving energy and enhances overall system performance.
- Higher Load Capacity: The helical design distributes the load more evenly across the teeth, allowing these gears to handle higher loads and stresses. This increases the gear’s lifespan and reduces maintenance requirements.
Our Manufacturing Process
At At Shanghai Belon Machinery Co., Ltd, we employ advanced technology and stringent quality control to produce helical gears that meet the highest standards. Here’s a glimpse into our manufacturing process:
- Design and Engineering: Our engineering team collaborates closely with clients to understand their specific requirements, providing customized design solutions that ensure optimal performance and compatibility.
- Material Selection: We use premium materials such as high-strength steel alloys and durable composite materials. These materials are selected for their ability to withstand high loads and resist wear and tear.
- Precision Machining: Utilizing state-of-the-art CNC machinery and precision cutting and grinding techniques, we achieve exceptional accuracy in gear dimensions and tooth profiles. Our machining process ensures that every gear meets exact specifications.
- Quality Assurance: Each helical gear undergoes rigorous quality testing, including tooth profile inspections, dimensional measurements, and performance evaluations. This meticulous quality control process guarantees the reliability and durability of our products.
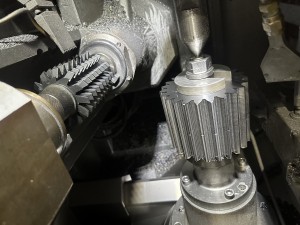
Hobbing Spur Gears
Hobbing gears is a machining process used to manufacture gears using a specialized tool called a hob. Usually hobbing process is more usual first teeth machining process to produce spur gears ,helical gears ,worm ...
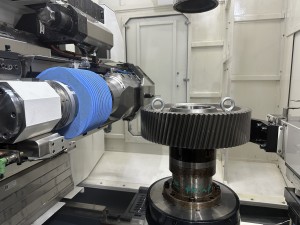
Grinding Spur /Helical Gears
Grinding gears refers to a machining process used to improve the accuracy and surface finish of gear teeth. The gear grinding machine is operated to move the grinding wheel and the gear blank relative ...
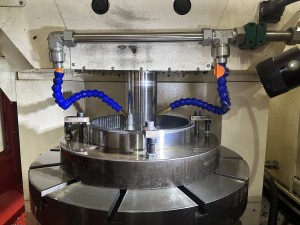
Shapping Internal Gears
Shaping internal gears is a machining process used to create the tooth profiles of internal gears. Internal gears have teeth on the inner surface and mesh with external gears to transmit power and motion betwe....
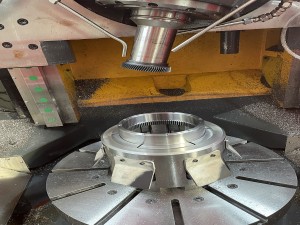
Power Skiving Internal Gears
Power skiving ring gears is a cutting-edge manufacturing process used to produce high-precision ring gears using the power skiving technique Power skiving is a gear cutting method that involves a specialized .....
WHY BELON FOR CYLINDRICAL GEARS ?
More options on Products
More Options on Quality
Wide Range of manufacturing methods hobbing ,fine hobbing ,grinding ,shaving ,shapping ,broaching ,power skiving
More Options on Delivery
Strong in house manufacturing along with top qualified suppliers list backup together on price and delivery competition before to you .