Gear tooth profile modification is a crucial aspect of gear design, improving performance by reducing noise, vibration, and stress concentration. This article discusses the key calculations and considerations involved in designing modified gear tooth profiles.
1. Purpose of Tooth Profile Modification
Tooth profile modification is primarily implemented to compensate for manufacturing deviations, misalignments, and elastic deformations under load. The main objectives include:
- Reducing transmission errors
- Minimizing gear noise and vibration
- Enhancing load distribution
- Increasing gear lifespan According to the definition of the meshing stiffness of the gear, the elastic deformation of the gear teeth can be approximated by the following formula: δa – tooth elastic deformation, μm; KA – Use factor, refer to ISO6336-1; wt – load per unit tooth width, N/mm,wt=Ft/b; Ft – tangential force on gear, N; b – effective tooth width of gear, mm; c ‘- single pair tooth mesh stiffness, N/(mm·μm); cγ – Average meshing stiffness, N/(mm·μm). Spur Gear
Bevel Gear 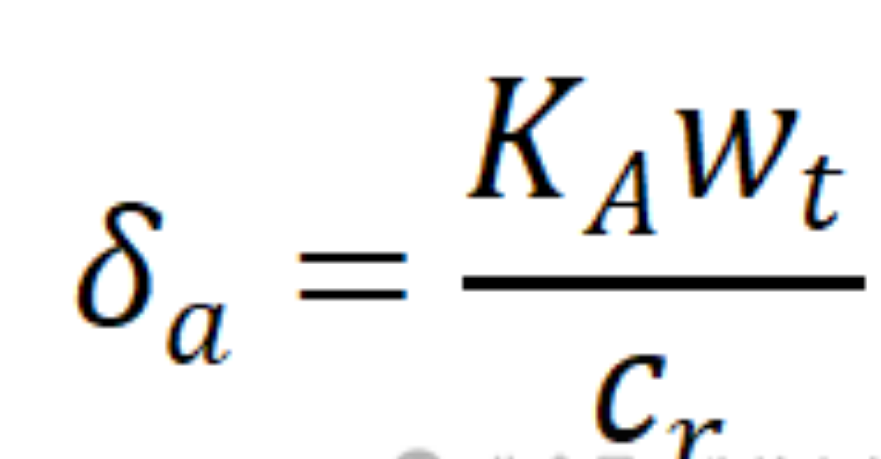
- Tip Relief: Removing material from the tip of the gear tooth to prevent interference during meshing.
- Root Relief: Modifying the root section to reduce stress concentration and enhance strength.
- Lead Crowning: Applying a slight curvature along the tooth width to accommodate misalignment.
- Profile Crowning: Introducing curvature along the involute profile to reduce edge contact stresses.
3. Design Calculations
Gear tooth profile modifications are typically calculated using analytical methods, simulations, and experimental validation. The following parameters are considered:
- Modification Amount (Δ): The depth of material removed from the tooth surface, usually ranging from 5 to 50 microns depending on load conditions.
- Load Distribution Factor (K): Determines how the contact pressure is distributed across the modified tooth surface.
- Transmission Error (TE): Defined as the deviation of the actual motion from the ideal motion, minimized by optimized profile modification.
- Finite Element Analysis (FEA): Used to simulate stress distributions and validate modifications before production.
4. Design Considerations
- Load Conditions: The amount of modification depends on the applied load and expected deflections.
- Manufacturing Tolerances: Precision machining and grinding are required to achieve the desired modification.
- Material Properties: The hardness and elasticity of gear materials influence the effectiveness of profile modifications.
- Operational Environment: High-speed and high-load applications require more precise modifications.
5. Tooth profile modification is essential for optimizing gear performance, reducing noise, and improving durability. A well-designed modification, backed by accurate calculations and simulations, ensures the longevity and efficiency of gears in various applications.
By considering load conditions, material properties, and precision manufacturing techniques, engineers can achieve optimal gear performance while minimizing operational issues.
Post time: Feb-11-2025