Worm gears and bevel gears are two distinct types of gears used in various applications. Here are the key differences between them:
Structure: Worm gears consist of a cylindrical worm (screw-like) and a toothed wheel called a worm gear. The worm has helical teeth that engage with the teeth on the worm gear. On the other hand, bevel gears are conical in shape and have intersecting shafts. They have teeth cut on the cone-shaped surfaces.
Orientation: Worm gears are typically used when the input and output shafts are at right angles to each other. This arrangement allows for high gear ratios and torque multiplication. Bevel gears, on the other hand, are used when the input and output shafts are non-parallel and intersect at a specific angle, typically 90 degrees.
Efficiency: Bevel gears are generally more efficient in terms of power transmission compared to worm gears. Worm gears have a sliding action between the teeth, resulting in higher friction and lower efficiency. This sliding action also generates more heat, requiring additional lubrication and cooling.
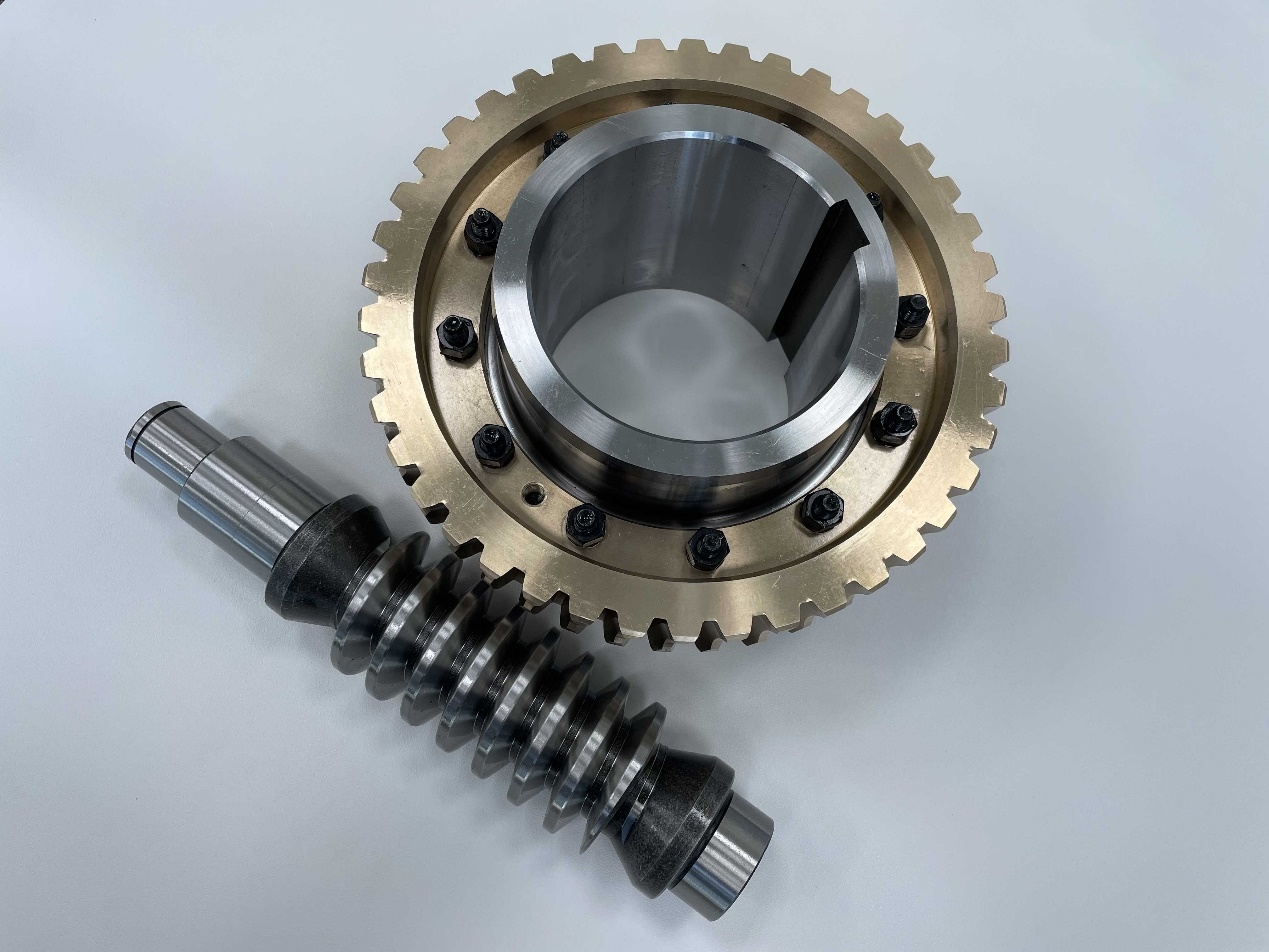
Gear Ratio: Worm gears are known for their high gear ratios. A single start worm gear can provide a high reduction ratio, making them suitable for applications where a large speed reduction is required. Bevel gears, on the other hand, usually have lower gear ratios and are used for moderate speed reductions or changes in direction.
Backdriving: Worm gears offer a self-locking feature, meaning the worm can hold the gear in position without additional braking mechanisms. This property makes them ideal for applications where it is essential to prevent backdriving. Bevel gears, however, do not have a self-locking feature and require external braking or locking mechanisms to prevent reverse rotation.
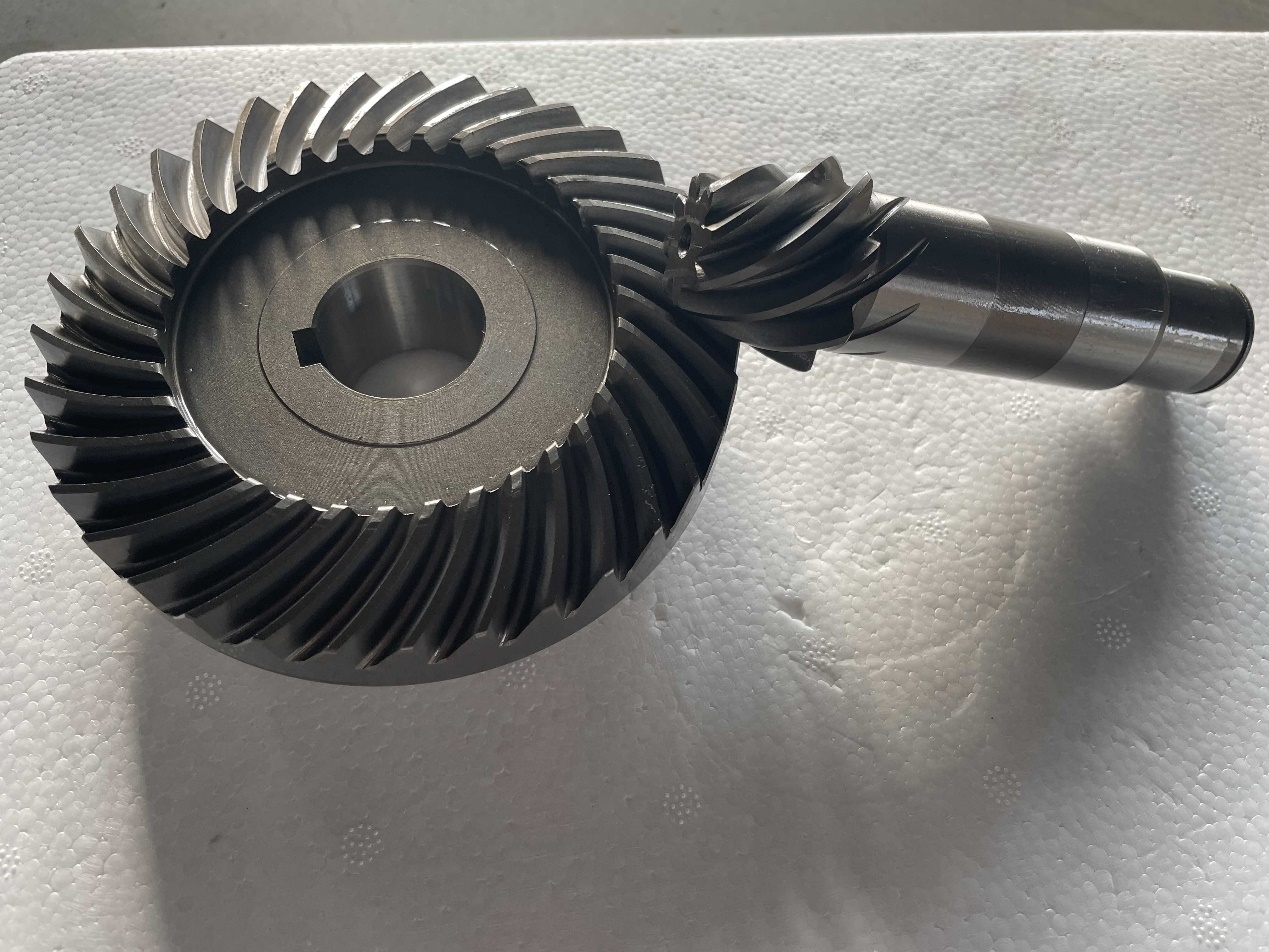
In summary, worm gears are suitable for applications that require high gear ratios and self-locking capabilities, while bevel gears are used for changing shaft directions and provide efficient power transmission. The choice between the two depends on the specific requirements of the application, including the desired gear ratio, efficiency, and operating conditions.
Post time: May-22-2023